Leading Roller Chain Manufacturer
Home » Roller Chain Manufacturer
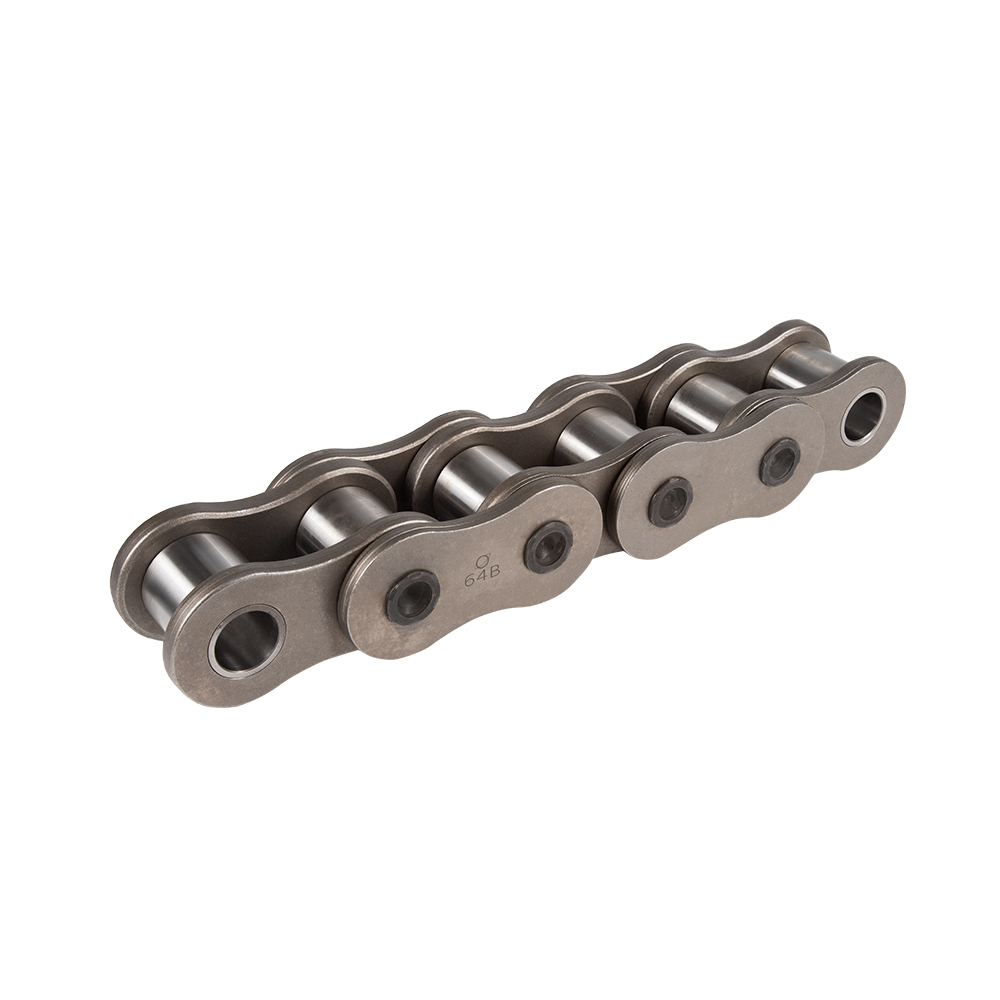
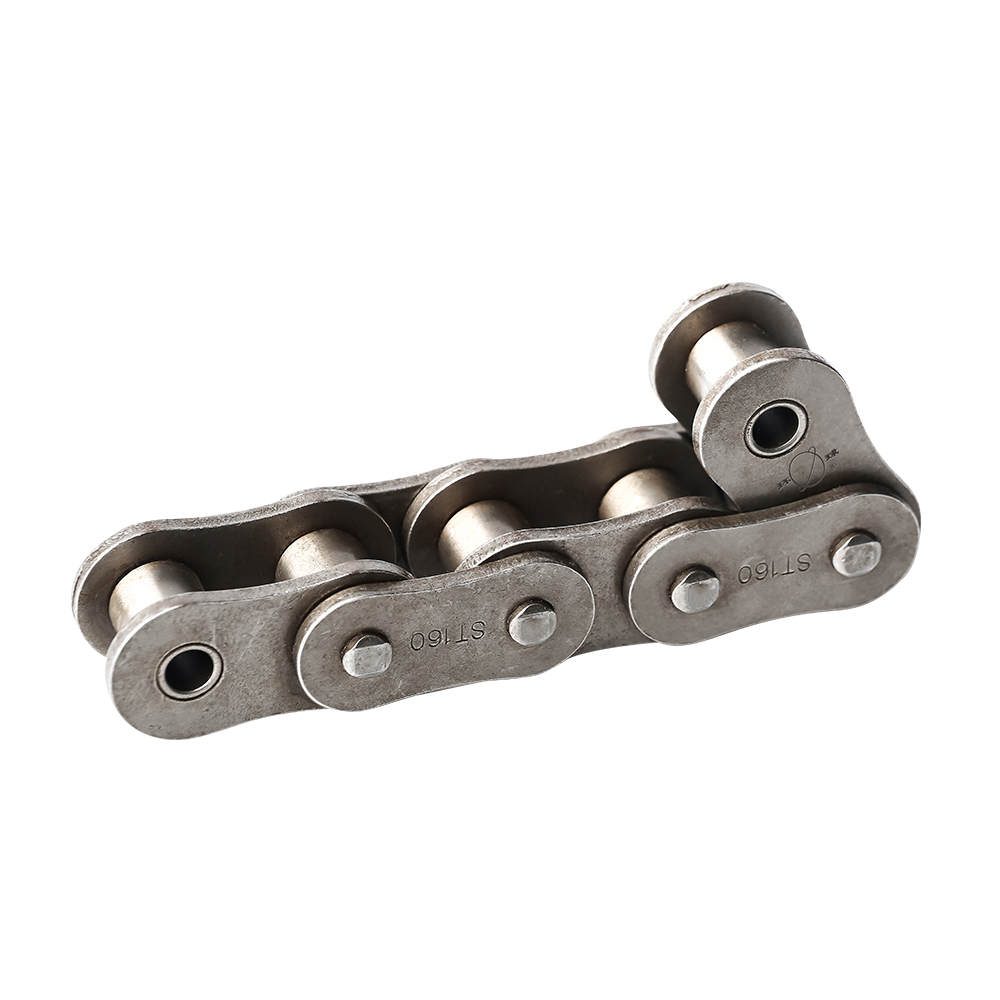
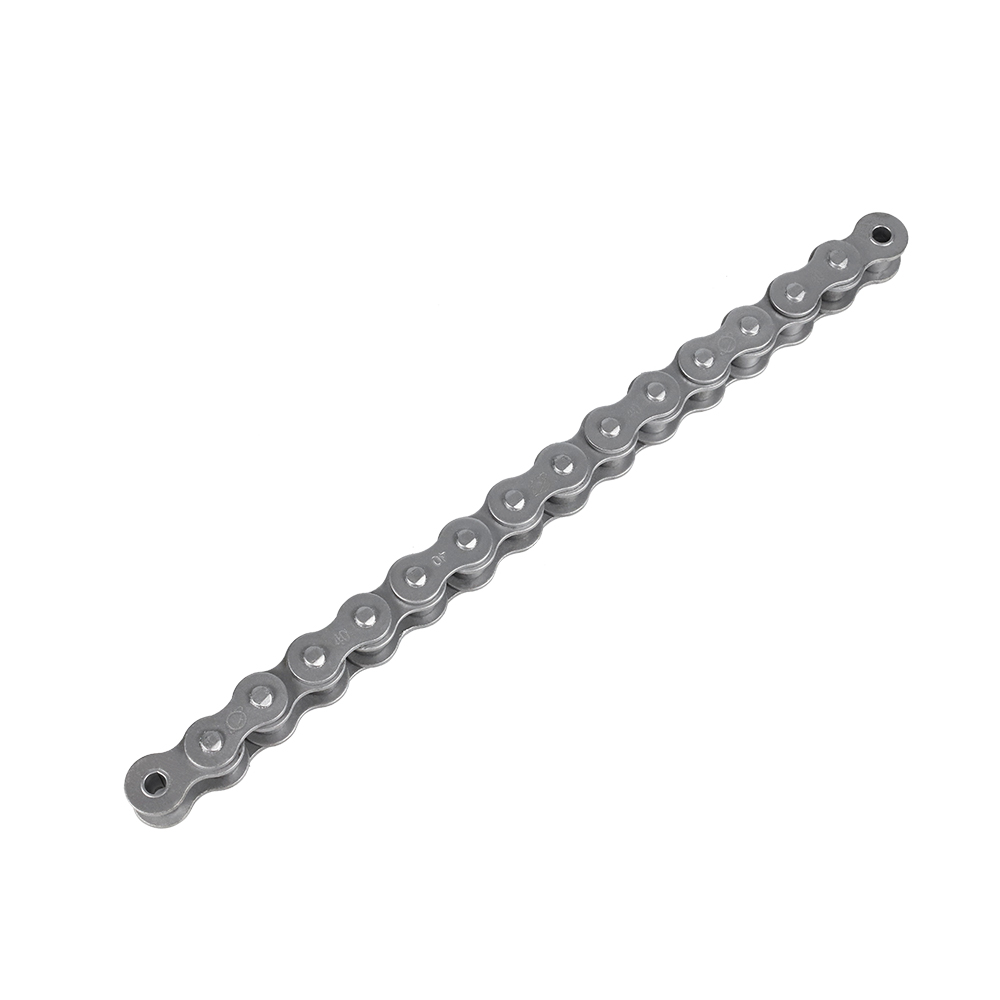
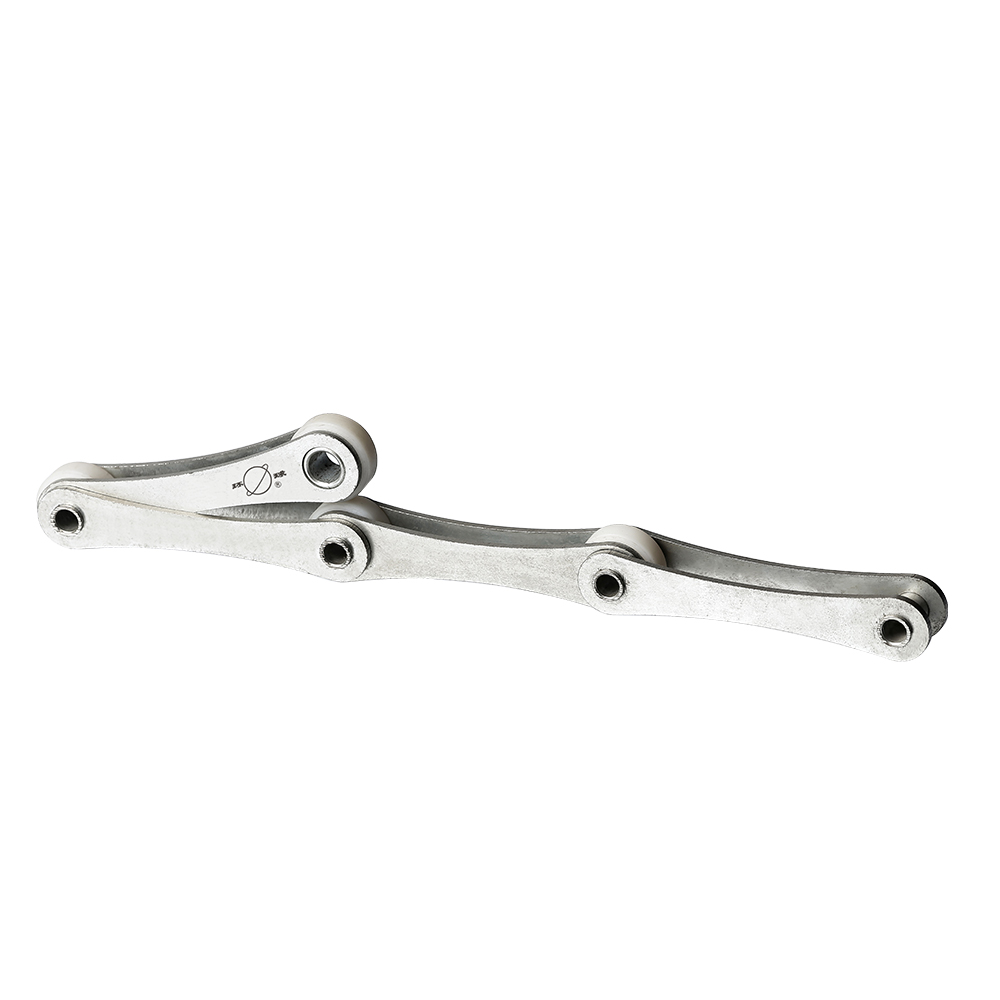
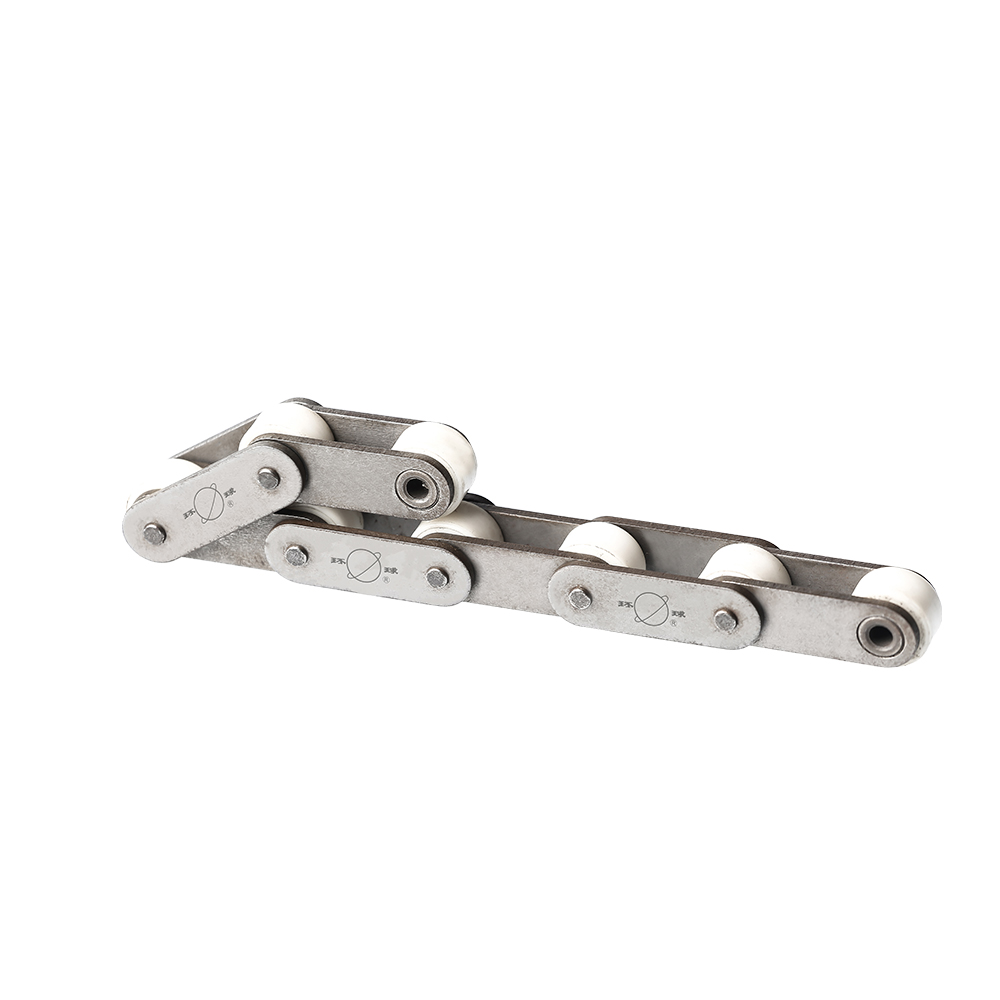
Universal Roller chains
The roller chain from Universal Chains has excellent wear resistance and corrosion resistance, and can operate stably for a long time in harsh working environments. Our industrial drive chains are the trusted choice for heavy-duty applications in industries like construction, mining, and metallurgy.
We can provide customized services according to the specific needs of customers to meet the personalized needs of different industries and scenarios. We can also derive special-purpose chains and enhance chain performance through special design and optimized processes.
Roller Chain Types
Precision Roller Chain
Mainly include A series, B series, reinforced type, cotter pin type and other series, which comply with ISO, DIN, ASME/ANSI and other standards
Double pitch transmission chain
Complying with ISO 1275, DIN 8181, ASME B29.100 and other standards, it is lighter and suitable for powering equipment with long conveying distances.
High strength short pitch precision roller chain
Comply with ISO, DIN, ANSI and other standards, adopt wide waist design, select high-quality materials and special heat treatment process
Self-lubrication roller chain
Complies with ISO, DIN, ASME/ANSI and other standards, and is dimensionally interchangeable with standard chains. Suitable for applications that require high wear resistance and cannot be maintained frequently
Features & Benefits
Materials
The product uses high-quality alloy steel materials and advanced technology to improve the strength and fatigue performance of the product, with some indicators reaching 1.1-1.7 times the ISO standard.
Quality certification
Products comply with international standards such as ISO, DIN, ASME/ANSI, etc., and have obtained industry certifications such as API, with reliable quality.
Customizable
Through special design and optimization processes, special-purpose chains such as sealed chains, lubrication-free chains, seamless hoses, and strong pre-zippers can be derived to meet the individual needs of customers.
Diverse products
including A series, B series, reinforced type, cotter pin type and other standard roller chains, as well as special chains such as motorcycle chains, double-pitch chain side bending (turning machine) chains, to meet the needs of different industries and application scenarios need.
Heat Treatment
Strictly control time and temperature, optimize material properties, and enhance the wear resistance and impact resistance of the transmission chain
Special surface treatment
Some products adopt surface treatment processes such as nickel plating and zinc plating to enhance the corrosion resistance of the product.
Tailored to Your Needs
- Tailored Design: At Universal Chains, we understand that every application is unique. Our team collaborates with clients to design chains that meet specific operational requirements and environmental conditions.
- Material Selection: We offer a wide range of materials, including specialized alloys and coatings, ensuring that each chain is optimized for durability, corrosion resistance, and performance in challenging environments.
- Rapid Prototyping: Need a quick solution? Our rapid prototyping service allows clients to test and refine designs before full-scale production, reducing lead times and ensuring satisfaction.
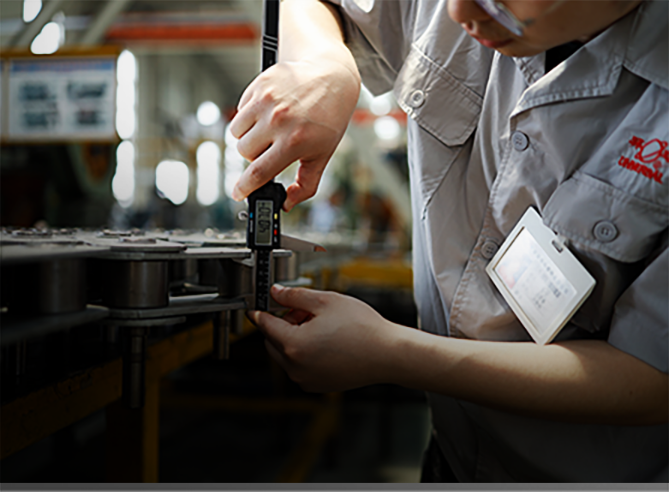
Manufacturing Process
- Heat treatment process: Quenching and tempering are used to enhance the hardness and wear resistance of the chain, so that it can withstand high loads and long-term use.
- Surface hardening treatment: Induction hardening or nitriding technology is used to improve the wear resistance and impact resistance of the chain surface.
- Anti-corrosion treatment: Passivation or electrolytic polishing is usually performed to enhance corrosion resistance. Passivation forms an oxide film to improve rust resistance; electrolytic polishing improves surface finish and reduces dirt adhesion.
- Coating technology: Add anti-corrosion or lubricating coatings to further enhance the corrosion resistance and reduce wear of the chain in harsh environments.
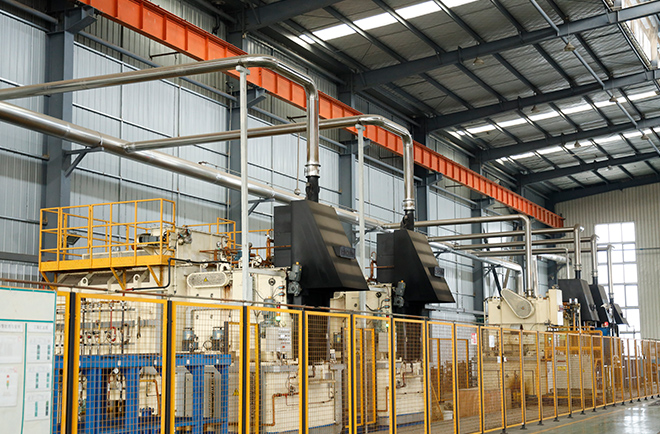
Inspection and Test Equipment
Universal has 50+ sets of various types of inspection and testing equipment for completed chains and chain components, which include 800KN fatigue testing machines and 600KW wear-testing machines.
We Love Our Clients
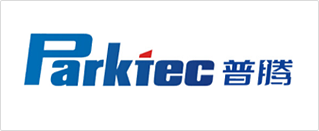
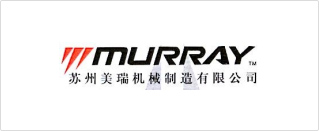
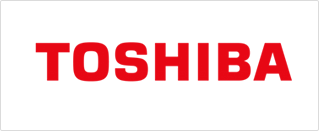
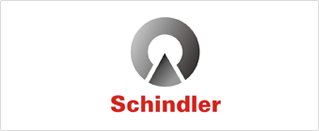
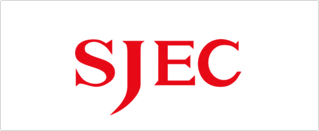
Application
Food processing and packaging
Cement Manufacturing
Agricultural Machinery
Engineering Machinery
Logistics and Transportation
Metallurgical Mining
Application
Food processing and packaging
Cement Manufacturing
Agricultural Machinery
Engineering Machinery
Logistics and Transportation
Metallurgical Mining
Related Products
China Roller Chain Manufacturer
Choose Universal Chains now, your trustworthy roller chain supplier, to make your equipment transmission more reliable and durable!
Frequently Asked Questions
What is the difference between roller chain and drive chain?
Roller chain is a special chain specially used for mechanical power transmission, mainly with cylindrical roller structure. Driving chain is a general term that covers various power transmission chains, including roller chains. In comparison, roller chains are lighter and more compact in size and weight, but have poor tolerance to harsh environments; Driving chains have high tolerance and are more suitable for harsh outdoor environments. A wide variety of driving chains allow buyers to choose based on specific application requirements such as load capacity, speed and environmental conditions.
What is the function of the drive chain?
The transmission chain is a key component of the mechanical power transmission system. Its main functions include: transmitting power from one place to another, connecting key engine components such as crankshaft and camshaft, achieving power input, output and speed change by meshing with the sprocket, and providing High strength, durability and other performance support to meet the needs of various industrial applications.
How are roller chains measured?
The main measurement parameters of the transmission chain include: pitch (distance between adjacent chain pin centers), roller diameter, plate thickness, total chain width, etc. These dimensional indicators jointly determine the load-bearing capacity and applicability of the chain, ensuring compatibility with components such as sprockets. Accurate measurement of these key parameters helps select the appropriate driving chain model to meet the needs of a specific application.
What is the strongest roller chain?
The strongest roller chains on the market today are usually made from high-strength alloy steels with excellent wear resistance and tensile strength. For example, ANSI standardized chains with models such as 10B-1 and 12B-1 are considered very strong choices for heavy-duty applications. Specific usage environments and load requirements also need to be considered when making a selection.
Ready to Order Universal Roller Chains?
Rest assured, your information is safe with us. We're dedicated to providing you with top-quality roller chains and excellent customer service. Place your order with confidence - your satisfaction is guaranteed!
Blog: How many types of roller chain are there?
Roller chain is an important component widely used in mechanical transmission systems, and its main function is to transfer power from one shaft to another. Due to its simple structure, high load carrying capacity and easy maintenance, roller chain is widely used in many fields such as industry, agriculture and transportation. According to different needs and working environments, roller chains can be categorized into various types, each of which has its unique advantages and applicable scenarios.
1. Standard single chain
Standard single chain is the most common type of roller chain, which is widely used in various mechanical equipment. It consists of a series of rollers and chain plates, which is suitable for general transmission needs and has good load capacity and wear resistance.
2. Heavy Duty and Extra
Heavy Duty Series
Heavy duty series and extra heavy duty series roller chains are designed to carry larger loads. These chains are usually made of high-strength materials and are suitable for use in heavy industry, mining and construction, etc. They can withstand extreme working conditions.
3. Double Pitch Chain
Double pitch chains have twice the pitch of standard single chains and are suitable for applications with long center distances. This type of chain is usually used in transmission systems to effectively reduce friction and energy loss, and is suitable for high-power equipment.
4. Self-lubricating chain
Self-lubricating chains are made of special materials or coatings that do not require additional lubrication and are suitable for use in environments where cleanliness or hygiene is important, such as the food processing and pharmaceutical industries. This design reduces maintenance costs and improves operational efficiency.
5. Plastic Chain
Plastic chains are made of engineering plastics and are lightweight and corrosion resistant. They are suitable for use in chemical environments or where there are stringent weight requirements, such as food processing, packaging and conveying systems. Plastic chains also have good impact resistance.
6. Silent Chain
Silent chain is designed to reduce the running noise, suitable for noise-sensitive environments, such as office buildings, hospitals and so on. This kind of chain usually adopts special material and structure design to reduce friction and vibration, so as to realize quiet operation.
Summarize
Different types of roller chains each have their unique advantages and application scenarios. When choosing, the most suitable type should be decided according to specific working conditions, load requirements and environmental factors to ensure efficient operation and long-term reliability of the equipment. The performance and efficiency of mechanical systems can be significantly improved through reasonable selection of roller chains.