Roller chains work hard across countless demanding applications, but their service life isn’t infinite. At some point, cumulative wear, fatigue and environmental factors cause functional failure. Knowing the root causes enables better prevention and lifecycle cost management.
- Fatigue from exceeded load capacity or runout
- Abrasive wear of pins, bushings and rollers
- Corrosive damage from chemicals or moisture
- Poor lubrication quality and contamination
While no two applications experience identical failure modes, a few common mechanisms tend to precipitate the end of a chain’s functional service. Let’s explore them in detail.
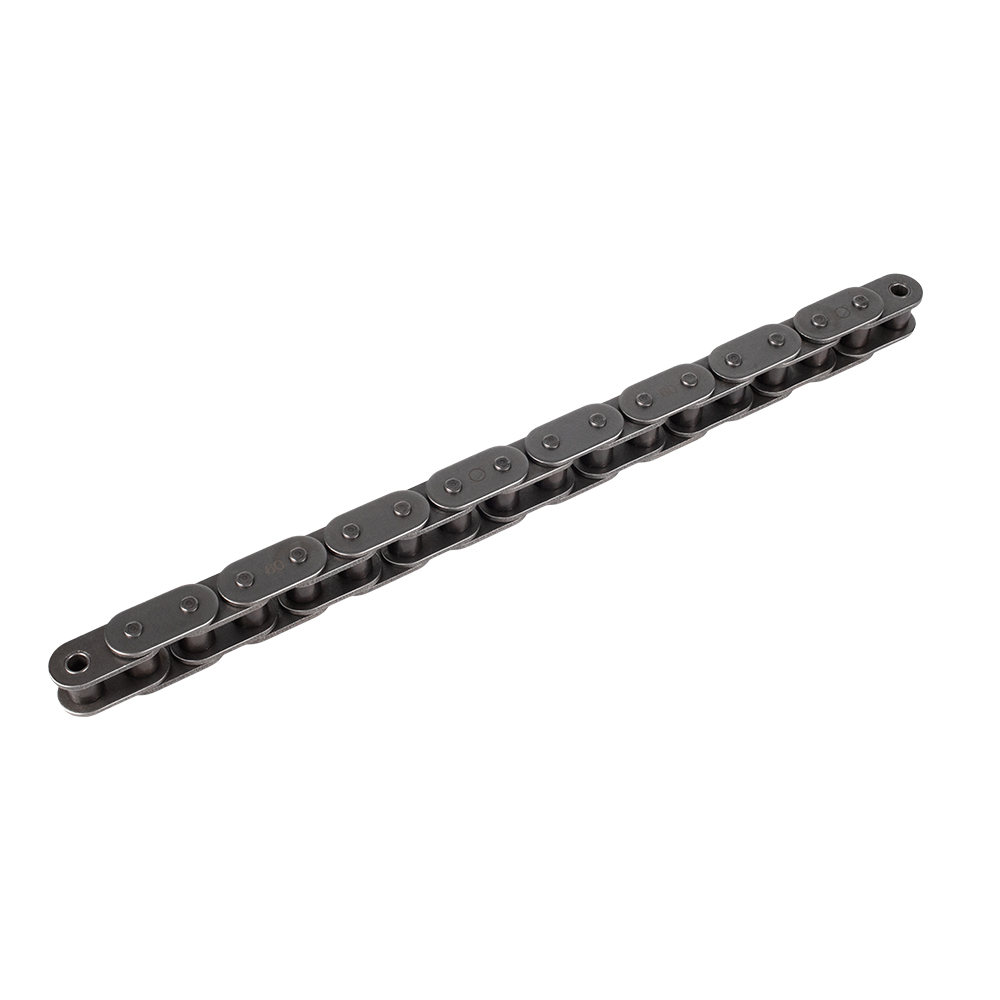
Roller Chain Problems – Causes and Fixes
Some of the main types of failure in roller chain are:
- Exceeding Fatigue Limits
One prevalent roller chain failure mode is fatigue stemming from loads or sprocket dynamics exceeding design limits over time. Signs include stretched or deformed plates, cracked rollers, and loose articulation.
Peak cyclic loads merely near the chain’s load rating gradually propagate tiny flaws from manufacturing or installation nicks. Once cracks form internally, complete failure typically follows soon after.
The smaller the sprocket diameter, the faster fatigue damage accumulates from flex stress. Insufficient center distance also strains chains around sprockets. Sudden overloading events further accelerate fatigue issues.
Proper chain sizing and lubrication helps control fatigue failure, as does switching to a stronger chain grade or larger pitch.
- Abrasive Wear
Another failure pathway involves abrasive wear of pins and bushings from contaminated environments or poor lubrication. As mechanical clearances grow from particle erosion, chain articulation suffers.
Overt signs include loose rollers, elongated holes, missing material on contact surfaces, and visible abrasive ingress. But well before visible issues, wear degrades efficiency and load capacity.
Improved filtration and lubricant retention helps slow abrasive damage, along with surface treatments like nickel plating. Periodic ultrasonic cleaning removes embedded particulates[1].
- Corrosive Damage
In wet, chemically aggressive or salty environments, corrosion poses roller chains trouble through microscopic pitting and cracking. These tiny surface defects serve as fatigue initiation points that grow into complete failure unexpectedly.
Discoloration, etching and surface irregularities indicate active corrosion and impending problems. But often, severe internal corrosion hides beneath intact exteriors.
Switching to corrosion-inhibiting lubricants and nickel plating alleviates damage while protecting against wear simultaneously.
- Contamination and Starvation
As the chain’s lifeblood, insufficient lubricant quantity or contamination also leads to failure. Without adequate lubrication, components grind away through metal-to-metal contact while fatigue damage accelerates.
Contaminants in lubricants like water, acids or particulates produce similar issues. The key is keeping fluids clean and plentiful. Automatic tensioners with reservoirs excel here.
Conclusion
Understanding the predominant roller chain failure modes makes it easier to mitigate through proper chain selection, lubrication methods and operating within design limits. Partnering with an application engineer upfront optimizes these factors for long, trouble-free chain life.
If you are looking for the best industrial-grade roller chain for your equipment, partner up with Universal Chains today!