Industrial chains are vital components used in various applications, from heavy machinery to conveyors and lifting equipment.
The manufacturing process involves several meticulous stages to ensure strength, durability, and reliability.
The systematic manufacturing approach combines traditional techniques with modern technology to produce industrial chains that meet rigorous performance requirements.
Each step—from raw material preparation to final testing and finishing—is carefully executed to ensure consistency and reliability in the finished product.
This commitment to quality ensures that heavy-duty chains are capable of withstanding the demands of diverse industrial applications effectively.
How Are Chains Made: 4 Vital Phases
Phase 1: Raw Material Preparation
The process begins with high-quality steel wire rods, chosen for their strength and durability.
These wire rods are uncoiled and fed through a guide ring into a draw box. Inside the draw box, the wire is lubricated with grease as it passes through a die.
This die reduces the wire’s diameter and increases its tensile strength, preparing it for the forming stage.
Phase 2: Forming the Links
Link Formation
The lubricated wire is fed into a forming machine where it is bent around a steel pin, creating a ‘C’ shape.
This initial shape is then closed to form a complete link. This process is repeated to create multiple links, each interconnected to form the chain.
Cutting and Shaping
Steel cutters notch the wire at predetermined intervals, marking where it will be cut into individual link-sized pieces.
A mechanized device then cuts the wire at these notches, and roller arms shape the cut pieces into precise links.
This ensures that each link is uniform and can securely connect with adjacent links.
Phase 3: Welding and Heat Treatment
Welding
Once formed, each link is welded together using an electrical process that fuses the ends of the wire without the need for filler material.
This welding step is crucial for ensuring the strength and integrity of the chain, as it creates a solid bond between the links.
Heat Treatment
The welded chain undergoes heat treatment to optimize its mechanical properties.
Initially, the chain is heated to high temperatures, approximately 1724°F, and then rapidly cooled in water.
This rapid cooling process, known as quenching, hardens the steel but can make it brittle.
To balance this, the chain undergoes a tempering process where it is heated to a lower temperature and cooled more slowly.
This secondary heat treatment imparts toughness and resilience to the steel, making it suitable for heavy-duty applications.
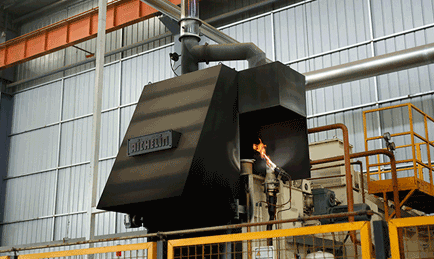
Phase 4: Final Processing
Calibration and Testing
After heat treatment, the chain is calibrated to ensure uniformity in link size and strength.
Samples are regularly tested to verify weld integrity and overall mechanical properties, ensuring compliance with stringent quality standards.
Finishing Touches
Depending on its intended use, the chain may undergo additional finishing processes such as:
- Shot blasting to remove surface imperfections
- Galvanizing for corrosion resistance
- Applying specialized coatings
These treatments enhance the chain’s durability and performance in challenging environments.
What are chains made of?
Chains, particularly industrial chains, are typically made of high-quality steel. This material is chosen for its strength, durability, and resistance to wear and corrosion.
The steel used in manufacturing industrial chains undergoes processes such as drawing and heat treatment to enhance its mechanical properties.
For specialized applications, industrial chains may also be made from materials like stainless steel or alloys to provide additional corrosion resistance or meet specific performance requirements.
Heavy-duty chains are specifically designed for applications that require exceptional strength and durability.
Industrial Chain Manufacturers: Universal Chain
Universal Chain is a prominent manufacturer known for producing a wide range of industrial chains tailored to various sectors such as mining, manufacturing, and agriculture.
They specialize in designing industrial chains that offer robust performance under demanding conditions, incorporating advanced manufacturing techniques to ensure reliability and longevity.
Universal Chain’s products, including heavy-duty chains, are engineered to meet stringent quality standards.
This makes them the preferred choice in industries requiring dependable power transmission and material handling solutions.
Their industrial chains and heavy-duty chains are essential for applications where strength and durability are paramount.