Industrial chains are made from either carbon steel or alloy steel chain, chosen based on their strength requirements and application demands.
If you’re searching for this, you likely need a chain for heavy-duty tasks—lifting, transporting, or powering industrial equipment.
The right chain material ensures safety, long-term performance, and cost-efficiency in your operations.
This guide walks you through the types of chain materials, how they’re made, and what makes them reliable.
Types of Materials Used in Industrial Chains
So what is chain made of? Here’s a look at the different materials industrial chain manufacturers use:
Carbon Steel
Carbon steel forms the foundation for most industrial chains. This material provides excellent durability for general applications and transport securement. Standard carbon steel chains handle weights up to 7,000 pounds, while heat-treated versions offer enhanced strength for heavy-duty transport.
Alloy Steel
Alloy steel chain contains additional elements like nickel, copper, chromium, or manganese. These materials increase the chain’s maximum breaking strength. OSHA requires alloy steel specifically for material handling and overhead lifting equipment. This material handles loads exceeding 35,000 pounds.
Surface Finishes
Industrial chains come in three different finishes. Each finish determines how well the chain resists corrosion and performs in different environments.
- Bright Finish (Self-colored): Carbon or alloy steel without coating. The metal remains exposed, which can lead to rust. This makes it less expensive but requires protection from moisture.
- Galvanized: A thin layer of zinc coats the metal. This coating prevents rust, scratching, and corrosion. Galvanized chains cost similar to bright finish but last longer.
- Stainless steel: Iron-based material with 10-11% chromium content. This finish naturally resists corrosion and gives chains a bright appearance. Stronger than other options but more expensive.
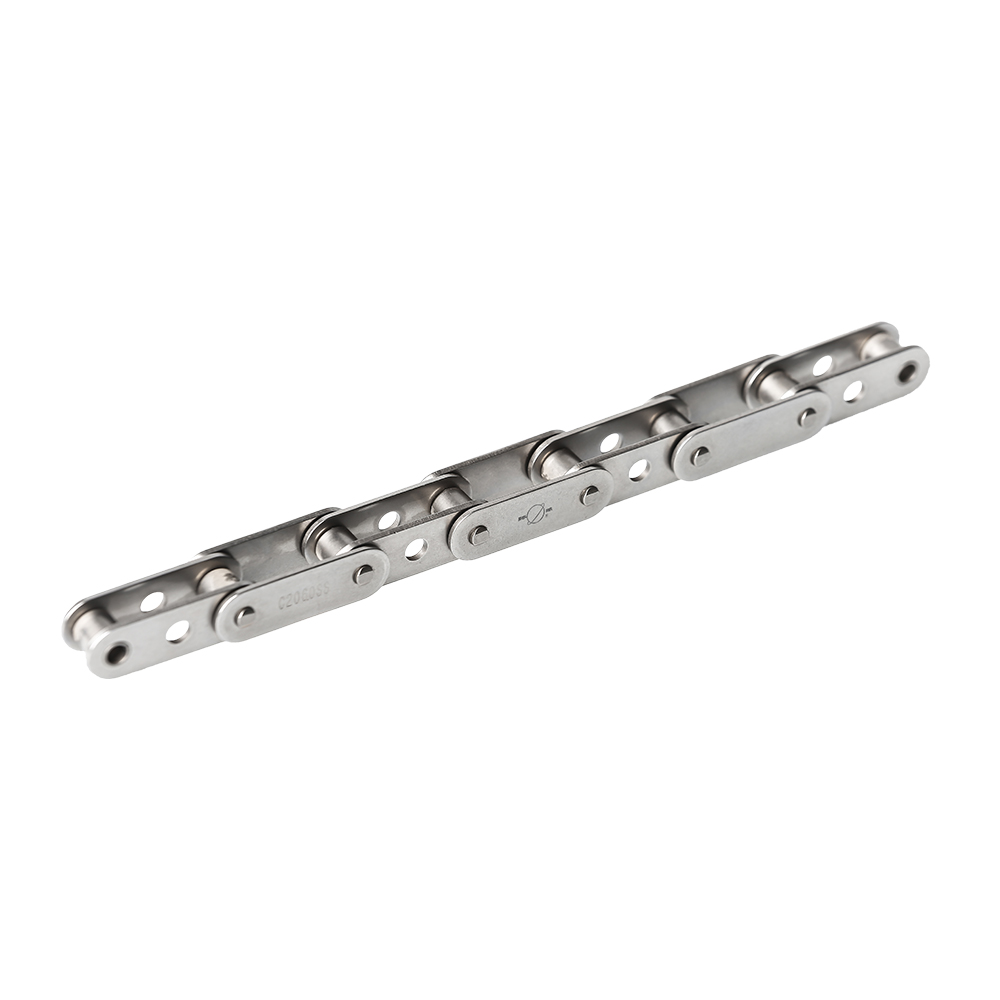
Manufacturing Processes
Industrial chain production requires precise control over materials and processes. Each grade follows strict manufacturing standards for consistent performance and safety compliance.
- Material selection: Base metals are selected according to grade requirements. Carbon steel serves Grade 30-70 chains. Alloy steel with nickel and chromium creates Grade 80-100 chains.
- Heat treatment: Each grade undergoes specific heat treatment processes. Grade 70 chains receive treatment to enhance carbon steel properties. Grade 80-100 chains need specialized heating for maximum strength.
- Forming process: Automated systems form chain links under strict dimensional control. This ensures consistent size and shape for proper operation in industrial equipment.
- Quality testing: Every chain must pass tensile strength tests for its grade rating. Grade 80 chains demonstrate 20% stretch capacity. Grade 100 chains prove their ability to handle loads over 35,000 lbs.
Frequently Asked Questions
What’s the strongest chain material available?
Alloy steel chains, particularly Grade 100, provide maximum strength ratings up to 35,000 lbs capacity. These chains combine superior material properties with advanced manufacturing processes.
When should I choose alloy steel over carbon steel?
Choose alloy steel when overhead lifting is involved or when applications demand maximum strength. OSHA requires alloy steel chains for all overhead lifting operations.
Do different materials require different maintenance?
Yes. Carbon steel needs regular lubrication and moisture protection, while stainless steel offers better corrosion resistance. Galvanized chains provide a middle ground with good weather protection.
How do I know which grade I need?
Consider your load requirements, operating environment, and safety regulations. Grade 30-43 suits general use, Grade 70 for heavy transport, and Grades 80-100 for critical lifting operations.
Conclusion
Selecting the right roller chain material directly impacts your operation’s success and safety compliance. As a leading chain manufacturer since 1970, Universal Chain combines advanced manufacturing capabilities with extensive material expertise to deliver reliable solutions.
Our state-of-the-art manufacturing facility produces over 60 million meters of chain annually, serving 10,000+ clients across 100+ countries. With our National Enterprise Technology Center and 100+ patents, we ensure every chain meets strict material and quality standards.For expert guidance on selecting the optimal chain material for your specific application, send us a message.