When it comes to transporting materials, drag chain conveyors are an excellent choice. They are efficient and reliable for moving bulk materials. However, the performance of these conveyors greatly depends on the quality of the drag conveyor chain or heavy-duty steel chains used. In this blog, we will explore what makes a drag chain conveyor successful.
Importance of Drag Chains in Conveyor Systems
Chains are crucial components in any drag conveyor design. They are responsible for transferring the force needed to move materials along the conveyor. Understanding the best chains for drag conveyors can significantly impact performance and efficiency.
Corrosion: A Major Concern
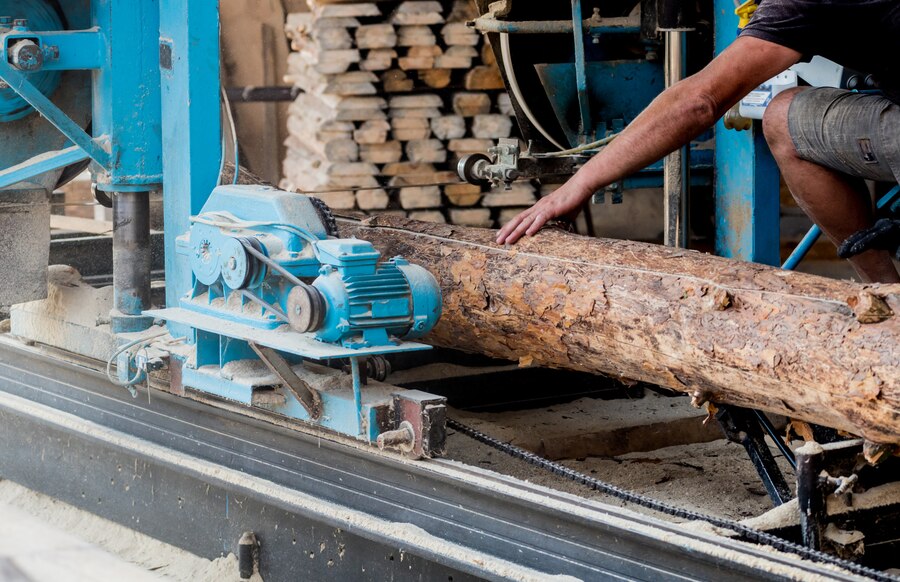
One of the most significant challenges for drag conveyor chains is corrosion. Chains carrying raw wood or wood pulp are especially vulnerable to corrosion due to the acidity of the wood. Over time, this corrosion can weaken the chain, leading to a higher wear rate.
The Impact of Corrosion
When the chain surface erodes due to corrosion, it becomes rough and abrasive. This rough surface can wear down adjacent parts more quickly. In many chains, the design assumes that other parts will fail before the pins. However, corrosion often causes the pins to fail prematurely.
To combat this issue, it is crucial to use materials that resist corrosion. At Universal Chain Link, we have designed our corrosion-resistant chains with larger pins. These pins are stronger than the sidebars. They are better suited to withstand harsh environments and vibrations. Running the drag conveyor chains outside the material path minimizes their exposure to corrosive substances. It extends the chain’s lifespan.
Mechanical Wear: Understanding the Risks
In addition to corrosion, mechanical wear poses a significant risk to drag conveyor chains. Mechanical wear occurs when the chain flexes and bends during operation.
Effects of Mechanical Wear
Mechanical wear is often accelerated by the corrosive materials carried by the conveyor. The outer parts of the chain may be cleaned of corrosion. However, the pins can still suffer from abrasive wear caused by surrounding materials.
To minimize mechanical wear, it’s essential to reduce the number of times the chain flexes. Conveyors are typically designed to run the chain along wear strips outside the material path. This design limits the movement of the chain and helps maintain its integrity. However, in single-chain conveyors, the paddles can bend the chain sideways, causing faster wear due to uneven loading.
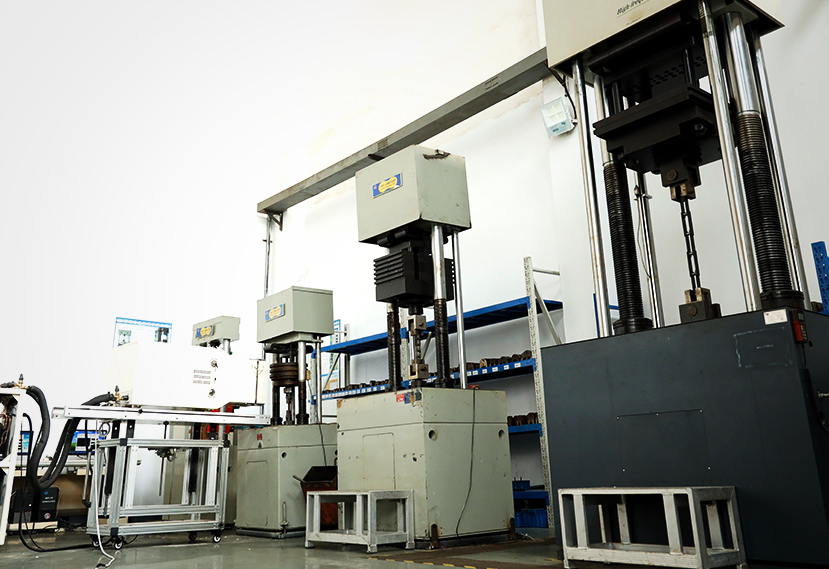
The Role of Friction in Conveyor Efficiency
Friction is another important factor to consider when evaluating drag conveyor chains. A good conveyor chain design aims for low friction.
Why Low Friction Matters
Low friction reduces the energy required to move the material and helps the conveyor run more efficiently. High friction can lead to increased running costs, as more energy is consumed to overcome the resistance. Choosing a drag conveyor chain with a design that minimizes friction is essential for long-lasting performance.
Strength Requirements for Drag Conveyor Chains
Understanding how strong a conveyor chain needs to be is crucial for selecting the right chain. Drag conveyor chains must handle the forces applied to them while maintaining a large working load relative to their weight.
Calculating Working Load
Businesses often calculate chain working loads differently. They consider various factors to determine how much load a chain can safely handle. This differs from calculating ultimate strength. That involves engineers determining the force at which a part will break.
Instead, working load is usually expressed as a percentage of the ultimate strength. This percentage can vary based on multiple internal factors. At Universal Chain Link, we prefer to work with conservative factors to ensure we do not overestimate our chains’ strength.
Choosing a chain with a high strength-to-weight ratio is ideal. A chain that can support high working loads but is too heavy (low strength-to-weight ratio) is less effective. Because it requires more energy to move the conveyor components.
Selecting the Right Chain: Cost and Efficiency
Selecting the right drag chain conveyor is crucial for achieving optimal performance. A poor choice can lead to increased costs, downtime, and energy consumption.
The Cost of Incorrect Chain Selection
If the chain is not suitable for the application, it can lead to frequent replacements, which can be costly and time-consuming. Also, a poorly designed chain may consume more energy to operate, resulting in higher operating costs over time.
Benefits of Quality Conveyor Chain Suppliers
Working with reliable conveyor chain suppliers is essential. This ensures you select the right chain for your application. Quality suppliers provide not only high-quality chains but also valuable expertise in selecting the best products for specific needs.
Why Choose Universal Chain?
When it comes to selecting chains for drag conveyors, Universal Chain stands out as a leader in the industry.
Advantage of Research & Development
Universal Chain integrates research, manufacturing, and marketing of chain products. Their National Enterprise Technology Center is essential for developing industry standards. It has also accumulated over 100 patents to promote innovation.
Advantage of Manufacturing
Universal Chain guarantees that each drag conveyor chain is produced with the utmost precision and quality. They have over 2000 high-precision production machines and 6 unique processing crafts. Their intelligent production management system helps maintain consistency and efficiency.
Advantages of a Quality Control
Universal Chain takes quality control seriously. They own large tonnage inspection and testing equipment. They follow complete quality control regulations. Their product quality traceability system ensures that every chain meets strict performance and safety standards.
Conclusion
Understanding the best chains for drag conveyors requires considering various factors. These include corrosion resistance, mechanical wear, friction, and strength. A drag conveyor chain that meets these requirements enhances performance and reduces operating costs.
By choosing high-quality chains from reliable suppliers, businesses can ensure they have the right equipment. Universal Chain is an excellent option for meeting specific application needs. Universal Chain has advanced research and manufacturing capabilities, along with strict quality control. This enables them to provide chains that withstand tough conditions. This ensures long-lasting performance and efficiency in drag conveyor systems.